Inigo & The New Craftsmen: willow basket weaving with Hilary Burns
The Devon-based artisan explains how her beautiful woven designs have been thousands of years in the making
- Words
- Nick Carvell
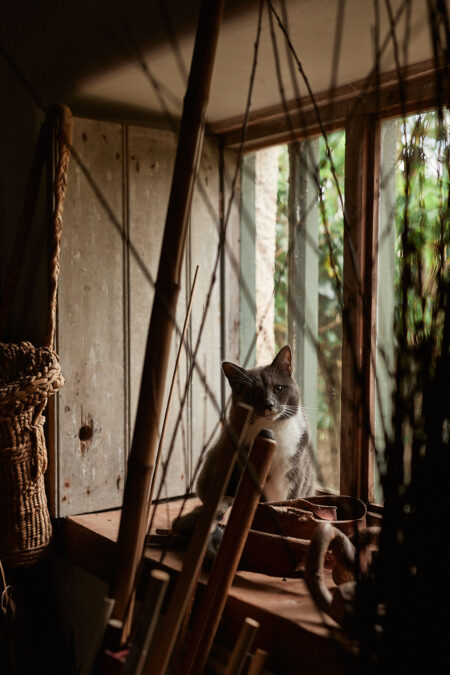
This article is the first in a new collaborative series from Inigo and The New Craftsmen, showcasing the work and processes of British designer-makers who find new inspiration in traditional craft techniques. Visit The New Craftsmen online to explore more of Hilary’s work, and browse an unrivalled selection of contemporary ceramicists, carpenters, blacksmiths and more.
Despite being one of Britain’s most respected basket-makers, Hilary Burns is the first to admit she ended up working with willow by default: weaving was always her first love. Inspired by playing with her mother’s loom and the local African grass crafts she saw growing up in Zambia, she first worked in a commercial knitting mill in Cape Town before leaving to study textiles at Middlesex Polytechnic in the early 1970s. It was while she was working as a weaving technician at Central St Martins in London that she took her first course in basketry out of pure curiosity – and she hasn’t stopped since.
She started making baskets full-time in 1985 when she moved to Devon with her husband and three children, and has continually worked with who she refers to as “the old boys” of the basket-weaving world to learn ancient techniques before they are lost. Today, in between creating human-sized willow busts of William Shakespeare for the British Museum and woven hoods for the stage, she enjoys nothing more than honing her craft by making useful items for people’s homes – and teaching the skills she’s learned to the next generation of weavers through her voluntary organisation, Basketry and Beyond.
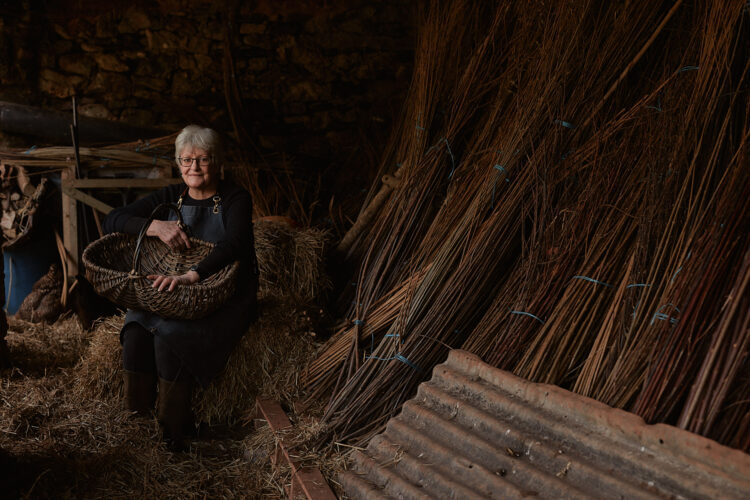

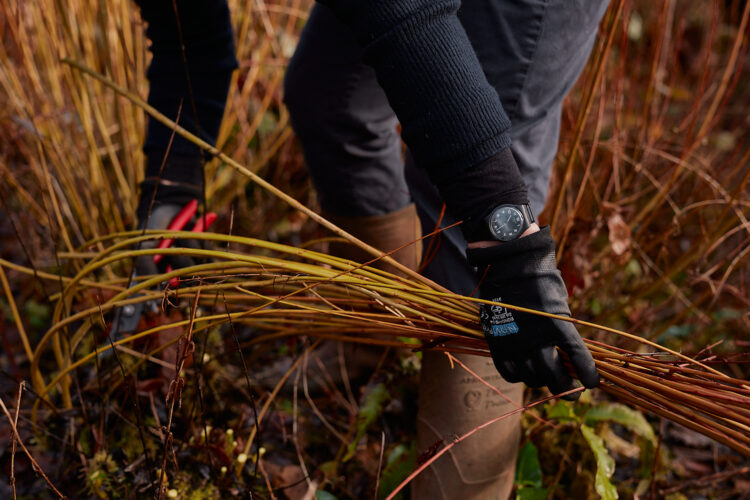
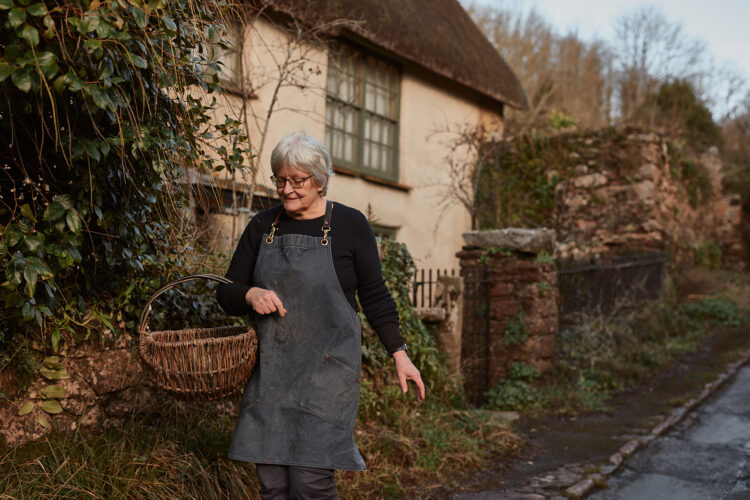
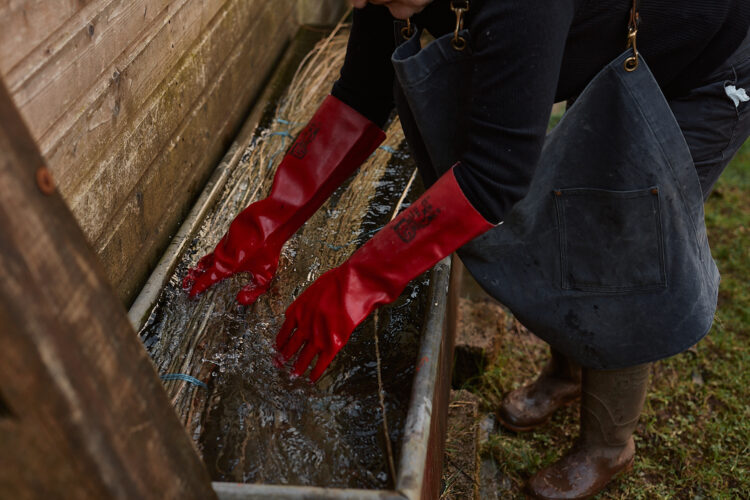
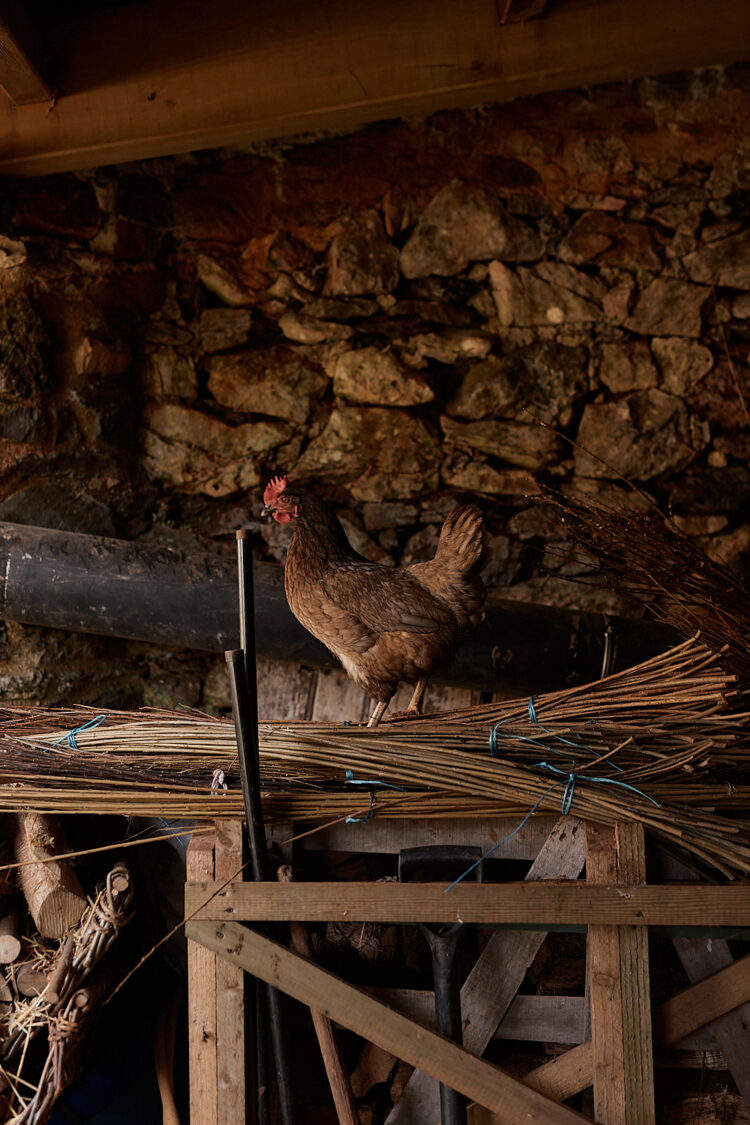
“When I was training, the courses I went on used very few British materials – and as my interest was primarily in English basketry techniques, I wanted to use homegrown willow. Sadly, while there used to be a huge willow-growing industry here in the UK, mainly centred in the East Midlands, by the time I started my business in the mid-1980s, there were only a couple of families in Somerset producing it. So, I started growing willow myself – and the beds I planted then, with cuttings from the National Willow Collection near Bristol, are the ones I still use today.
“I start the process of making a basket by cutting the willow from my beds. I then grade the sticks by size, bundle them and put them in the barn to dry. You can work with semi-green materials, but they shrink, so it’s better to dry them, then re-soak them to make them flexible when you need them.
“Depending on the type of willow and the size of stick, re-soaking can take anything up to ten days; even longer in the case of the reddish willows. You can tell when they’re ready as you’ll be able to wrap the end around your wrist. Then I put them in a cloth overnight so that any water on the surface is driven into the middle. After this, they shouldn’t feel wet, they should feel pliable.
“For each stage of the basket you need different sticks: thick sticks for the base (stakes) and thin weavers for the sides. It’s all about selection and being able to tell the difference between sizes, as this can be miniscule. It’s done by eye and by feel – like a cigar!
“I am quite an impatient person, but weaving forces you to be patient.”
“While some techniques require a full framework to be created first, most of my basket work calls for the base to be made first, then the sides attached afterwards. After you’ve created your framework, it’s a matter of weaving slimmer sticks around this in a circular motion. The tricky thing is that you have to think about space in three dimensions as you weave – so you’re looking at the place your fingers are in the pattern, but you’re also looking ahead to where your fingers need to end up, and making small adjustments as you go to make sure the rows stay even.
“After the bottom and sides, the body of the basket is finished by working on the borders, which are woven from the uprights you used to create the base. I tend to make rod borders, which are a very British thing – I don’t do fancy plaits. All other things like handles, latches and lids are completed separately and go on afterwards.
“Then you need to let the basket dry – I put mine in the airing cupboard. After that I singe off the little fibres on the dried willows if necessary, but I don’t treat it with anything.
“I am quite an impatient person, but weaving forces you to be patient. If you make a mistake you have to unpick the entire thing carefully. There aren’t quick fixes in weaving, whether textiles or basketry – it’s all about taking the long view.
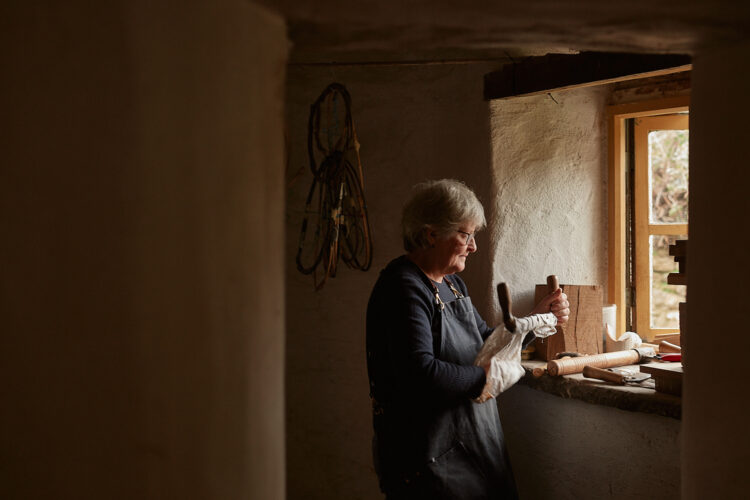
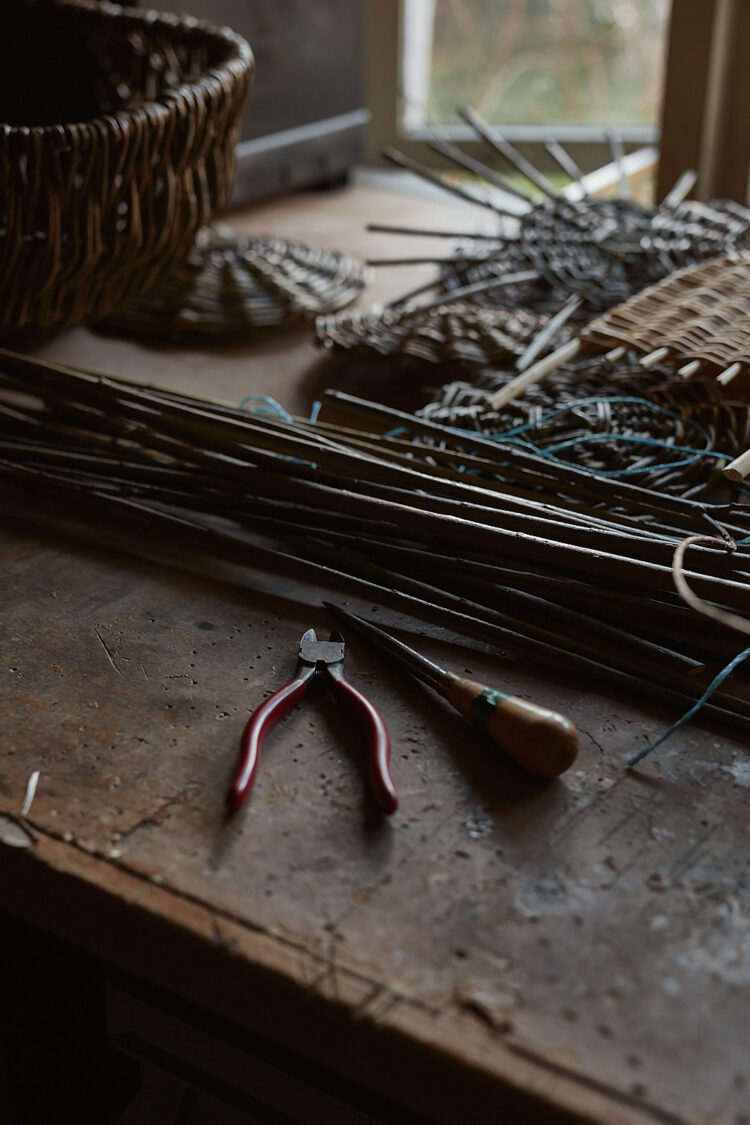
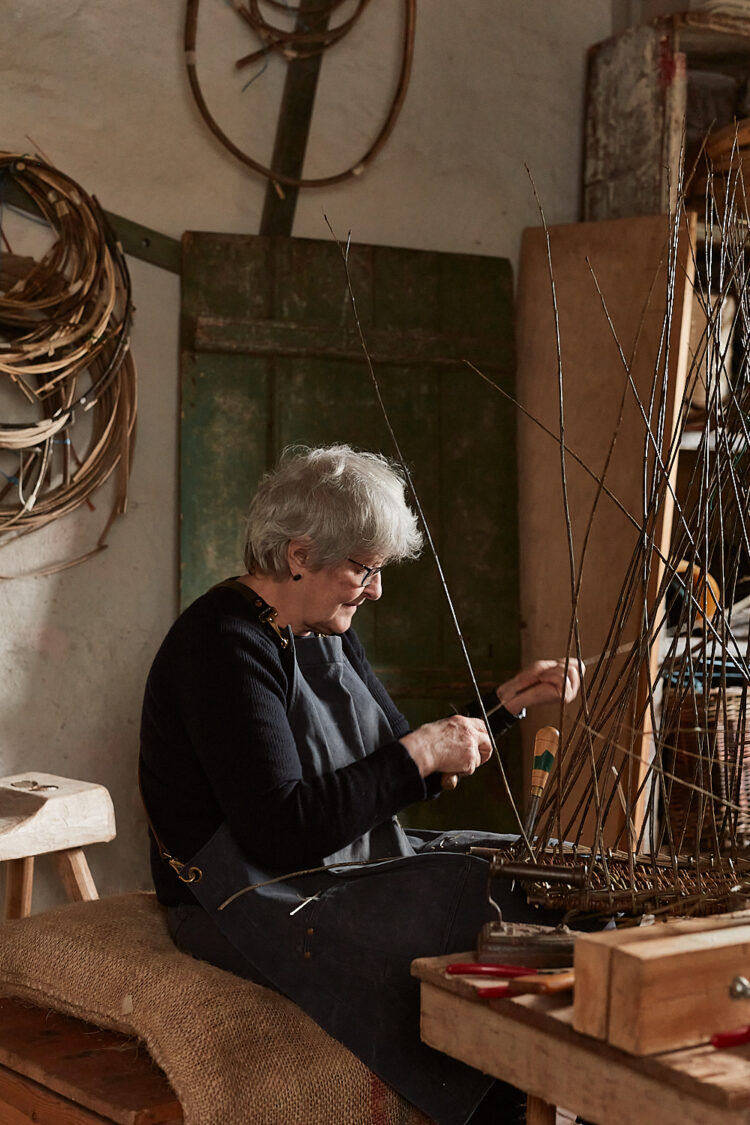
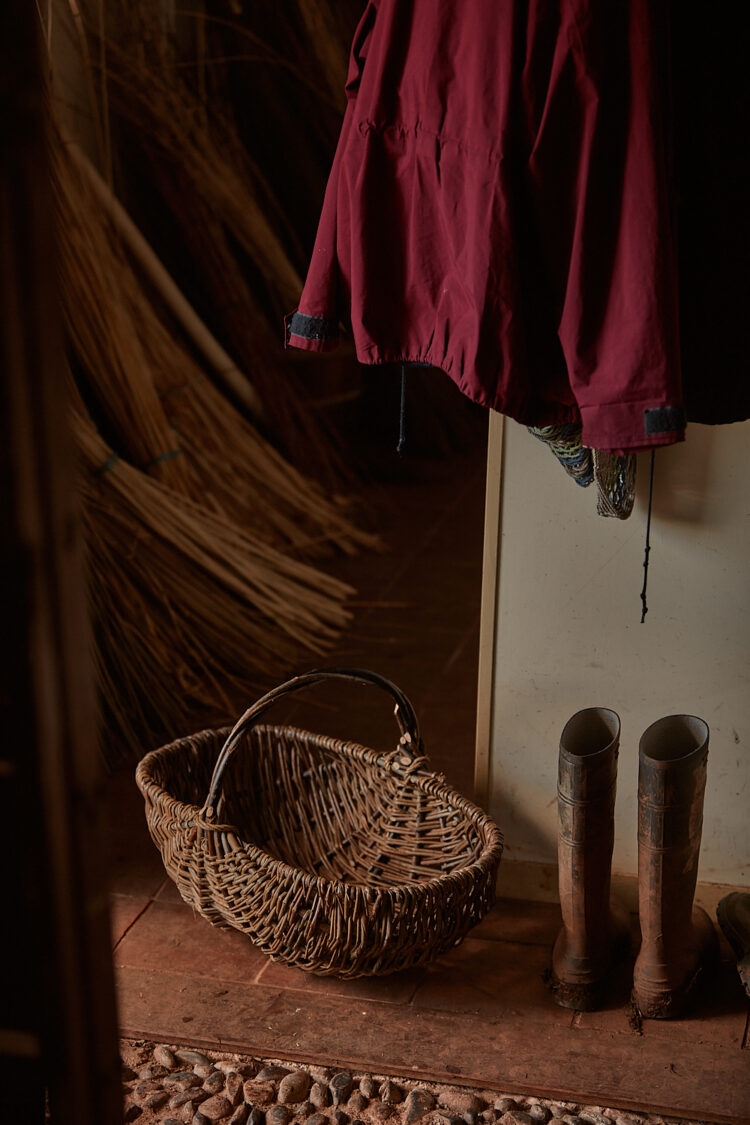
“I don’t really think there’s ever anything new, we’re just reinterpreting things.”
“I like to make useful things. During lockdown I’ve had a lot of requests for vegetable tubs, bread baskets and other things for the home from my customers, which I love crafting. I also like chair seating projects. I have done a few collaborations with interiors people – I did some seats recently with furniture-maker Ambrose Vevers. These were very time consuming as it’s so fiddly working out spacings, but when I’ve made a chair seat it’s ultimately very rewarding.
“I would love to explore more architectural projects before I retire – [to see] how weaving can fit into the built environment now in a similar way to how wattle and daub construction did in the past. I think basketry techniques have a lot to offer outside of baskets.
“I don’t really think there’s ever anything new, we’re just reinterpreting things. When you go back, you find a connection to today. As a basket-maker, I need to use those time-honoured techniques to make something that’s relevant to how the world is at the moment.”
Further Reading
Hilary Burns on The New Craftsmen
And there’s more…
Subscribe today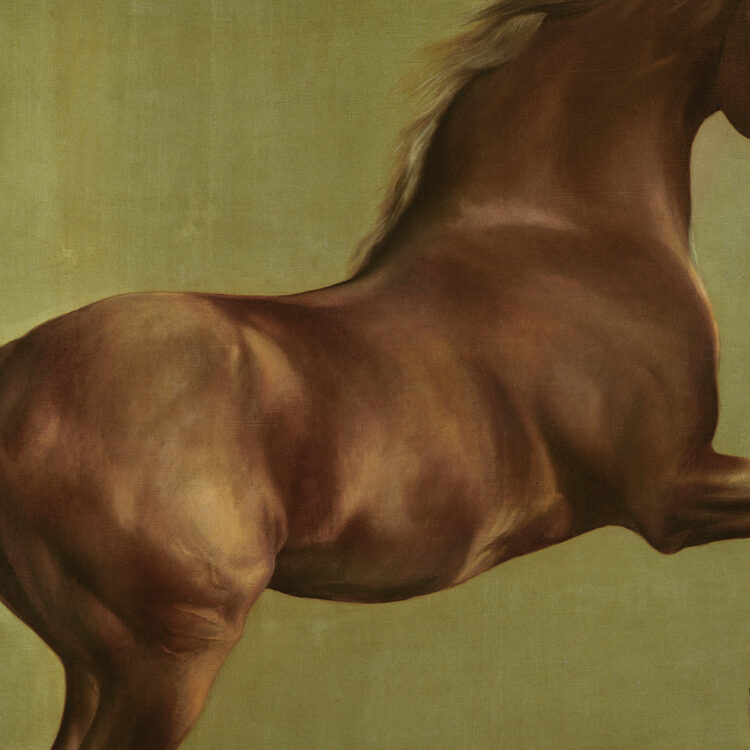
- The Handmade Home: creative courses to try in 2025Pursuits
- Let’s go outside: seven homes perfectly positioned for cobweb-blasting country walksHomes / Interiors / Pursuits
- Deck the halls: the jolliest open houses to explore this festive seasonInteriors / Pursuits
- Pick of the Bunch: Britain’s best pick-your-own flower farmsGardens / Pursuits
- Season’s Eatings: the country’s best garden restaurantsGardens / Pursuits